Custom Telescope Cases from Image Alloy Cases
Beginning in the mid-to-late 2000s, Celestron supplied its 8-inch SCTs without a case, which was surprising considering that Celestron’s signature scope was marketed as a portable telescope. Indeed, the C8’s impressive portability-to-aperture factor was why I bought it. After exhausting other ideas, I decided to explore having a custom case made.
My first approach to a custom-case manufacturer was somewhat disappointing – I was not happy with their product or its price. Fortunately, I continued my search and eventually discovered Image Alloy Cases in Welshpool, a suburb of Perth in Western Australia. The quality of the custom cases made by Image Alloy Cases (IAC) was far superior to anything I had previously seen, and they were also reasonably priced.
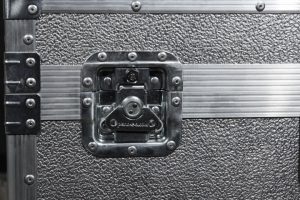
My main reason for wanting this level of protection for my telescopes and accessories was to mitigate the cost of insuring that equipment against damage, such as in the event of a motor vehicle accident to or from a dark-sky site. The ongoing annual insurance premiums were just too prohibitive.
The solution I decided upon was to have custom telescope cases made that fully protected, as far as practicable, my astro-tech investments. My research identified instances in which IAC cases had themselves been damaged in vehicle rollovers, such as at mine sites, while their contents remained undamaged, and closer inspection revealed why: Their precision-cut high-density foam inserts eliminated movement within the cases. I was impressed! That was the level of protection I wanted for my astronomical gear.
Image Alloy Cases has created 3 aluminium custom telescope cases for me. The material they used to form the cases is a thin marine ply with an aluminium laminate skin, to keep weight down. This material is strong and durable and has an
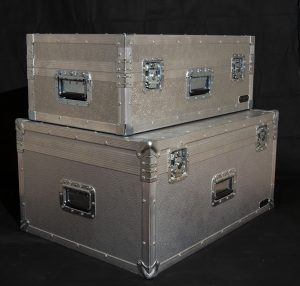
attractive stucco-texture finish. IAC cases are built to customer specifications, and a comprehensive range of options is available. My specifications required recessed, lockable butterfly locks (all cases are keyed alike for convenience) shown in Image 1, reinforced edges, reinforced corners, and spring-loaded recessed handles on the front and either end of each case (Image 2).
Internally, high-density foam was precision cut to protect each of the custom telescope cases inside the case to ensure that the scope and accessories could not move. The internal design is such that much of the telescope is assembled making for an easier and faster setup time. The case IAC built for my William Optics FLT110 Apo (Image 3) demonstrates how the internal setup can be designed to suit your needs. Everything I need with this telescope is in the one case.
Each of my telescope and accessory cases has a toolkit (Image 4), which varies from case to case. Two of these are shown in Image 3 secured in a cavity formed for that purpose in the foam insert of the WO FLT110 case. There are some duplications of items over the cases, for convenience, which far outweighs the small additional cost. An additional advantage is that everything has its place you can see what is missing and thus minimize the likelihood of something being left behind, which I have previously done.
For smaller telescopes and accessories, I use budget hard-plastic cases, rather than Pelican cases, which are more
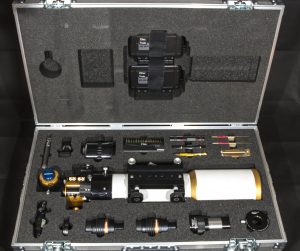
expensive. I don’t handle these cases daily, so considered the budget cases to be more than adequate for the job, and they have been.
A two-tier system was designed by Image Alloy Cases to accommodate the number of accessories I wanted in each case. Where necessary, an inner lid was utilized. The internal material is all high-density foam, which is machined precisely to fit the accessories. The top tier is glued to a 3.25-mm thick vinyl sheet base with two webbing tabs securely attached to the vinyl sheet base to lift out the top tier. The bottom tier stores the least used items. I have been using this system for some time now, and the arrangement works very well.
The DayStar Quark solar case and the two Tele Vue eyepiece cases (Images 5) use the two-tier setup, with the least-used accessories and the small tool kit on the bottom tier. Items are nestled, where possible, so little space is wasted. For example, the inverted Thousand Oaks glass filter has a high-density foam insert with a cutout for a 2.0-inch continuum filter, which sits above the glass surface of the white light filter, so there is no risk of damage to the surface of the filter. I use the continuum filter with the white-light filter, which is why I chose to store them together. The Astro-Tech AT65EDQ, plus DayStar Quark, serves as my solar telescope, with the addition of the Energy Reduction Filter.
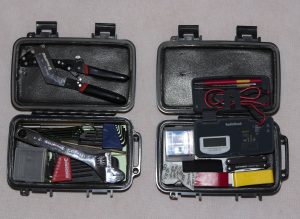
These cases were designed to accommodate eyepieces without end caps – I didn’t want to have to mess about with caps in the dark, particularly since, when closed, this case is moisture proof and dust proof anyway. The precise machining of the high-density foam mitigates the need for the end caps. Not having caps is great. In the dark, I can choose and replace eyepieces without looking or having to deal with end caps.
These custom-built cases are professional, strong and robust. There is a lot of work that goes into making an aluminium case, and designing and machining the high-density foam inserts for the interior of both the aluminium and hard cases. This quality and durability comes at a price though, but the price is quite reasonable when you consider the prohibitive cost of insurance against damage to the components they secure. The larger aluminium cases are around the price of a quality premium eyepiece, while the smaller hardshell cases come in around the price of a quality mid-range eyepiece. The prices include all materials, design, machining, and fitting of the interior of the cases.
Add up the value of the gear in these cases, the cost is indeed quite reasonable. Most of us invest a lot of ourselves in astronomy equipment and little on properly protecting and storing it. I have not regretted spending the money to ensure
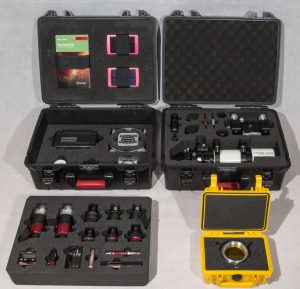
that my equipment is well protected, as I certainly cannot afford to replace all of it in the event of a catastrophe.
My case manufacturer is Image Alloy Cases, 44 Pilbara Street, Welshpool, WA 6106. Phone: (08)9258 7599. The proprietor is Jez Moore. This company is a professional case manufacturer, which specializes in custom instrument cases for the costly equipment sued by mining companies.
Author Peter Crake is a First-Class Machinist by trade and was later employed as a Production Manager and as a Technical Sales Engineer. Peter retired from the workforce in 2016 after five years service as an Academic Support Officer with Disability Services at a local college. An amateur astronomer for over 40 years, Peter has also collaborated on scientific research projects at Perth Observatory in the nineties. Peter is currently studying for a Bachelor of Arts (Photography) at Murdoch University in Western Australia.